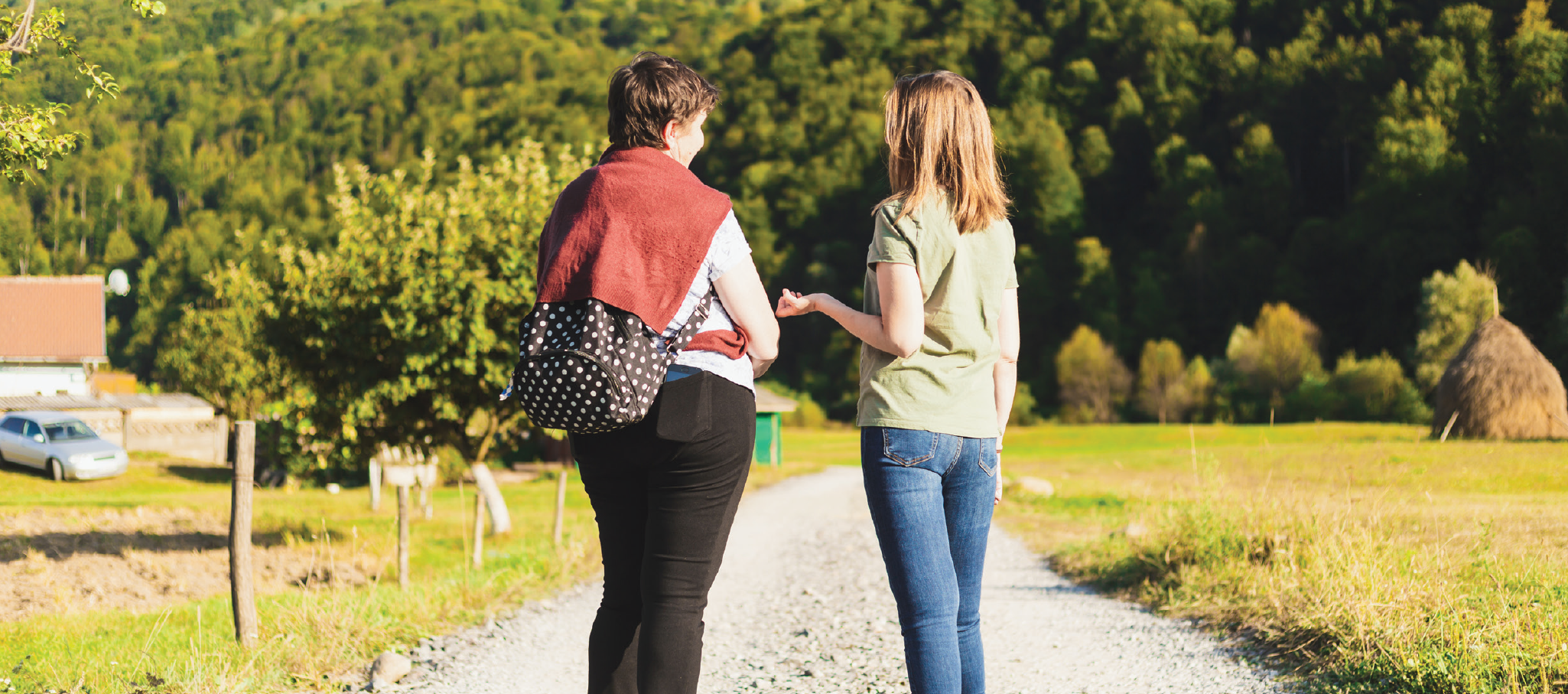
Elphinstone is a world leading OEM of above and underground mining equipment, passenger buses and electrical harnesses. It exports to over 30 countries and was the original developer of what is today Caterpillar’s hard rock underground mining equipment range.
Elphinstone had entered into an agreement with a new customer, Hanwha Defense Australia to manufacture its Howitzer design tank bodies and turrets as key sub-assemblies for the Huntsman class tanks that the multinational defence prime will supply to the Federal Government. To supply Hanwha, it was a requirement that Elphinstone’s Quality Management System (QMS) was certified to the ISO 9001:2015 standard. The time frame was very tight, just four months, but critical for Elphinstone to secure the multimillion-dollar Huntsman contract as well as a significantly larger follow-up contract to manufacture bodies and turrets for 440 Redback Infantry Fighting Vehicles.
1. Identify all key stakeholders within Elphinstone across the business function areas of engineering design, purchasing, fabrication, assembly, finish, shipping, IT and HR.
2. Undertake an ISO 9001 certification gap assessment via:
• Group sessions;
• One to one interviews with key people in each business function;
• Review of existing QMS documents;
• Factory floor walk-arounds and informal discussions with factory floor team members.
3. Once the gaps were identified, Project Lab consultants developed system and documentation changes to close the gaps and assisted the Quality Manager and other key people to implement the gap closing solutions.
4. Oversee and assist Elphinstone with the company’s first internal audit of the QMS as a whole.
5. Present on the day of the external accreditation audit to provide articulation, guidance and assistance.
“The support and advice Elphinstone received from The Project Lab was instrumental in securing our ISO 9001:2015 certification. With their guidance and assistance, we achieved certification in a remarkably short time frame and with zero non-conformances from our initial assessment - an outstanding result." - Ben Sandow, General Manager
CONSULTANTS
A key to successful delivery is matching the best consultant to the project. This is where The Project Lab gets it right and is able to draw on the diverse sector and expert domain experience and skills of its consultants.
This project was delivered by Jason Bresnehan and Greg Turner.